Stress tested: What to consider when looking at high-stress standard components
With processes becoming more efficient and manufacturing outputs expected to grow over the coming decade, it’s now more crucial than ever that standard components can withstand extended and prolonged use. Marcus Schneck, CEO of norelem, delves into the importance of implementing parts capable of withstanding high-stress to prevent downtime.
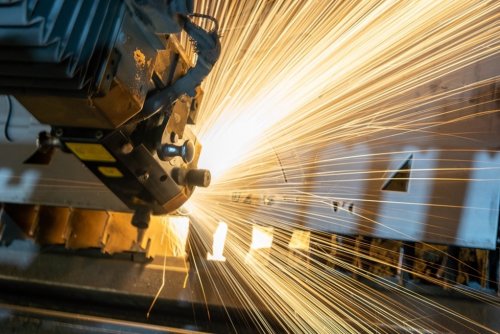
As we’re all aware, equipment and machines are susceptible to breakages, causing errors and delays. All components will eventually wear, tear, corrode or just reach a point of failure, often halting production and affecting the ability to maintain a high output throughout the year.
However, there are simple choices engineers can make to help combat the problem and mitigate the issue. By designing machinery with high-stress standard components in mind, machinery can go longer, failure rates can be lowered, and durability and reliability can be improved to withstand the forces and daily rigours involved in modern manufacturing.
Common Component Failures
There are numerous reasons why components fail, but it’s important to understand the most common component failures to help prevent slowdowns in production.
Often, electronic components are the first parts to fail within a system as they must not only be structurally sound in construction, but also perform digital functions. With potential failures found in soldering, packaging and distribution, manufacturers will usually implement a ‘burn-in’ period for several hours to ensure the component performs as expected.
However, the delicate nature of these parts means they’re quite suspectable to malfunctions and require regular maintenance to ensure consistent delivery of their programmed functions. Failures can be dependent on moisture levels, temperature fluctuations and power surges, which can not only stop production but also put a heightened mechanical strain on the system.
With that said, while maintenance is crucial to the prevention of equipment failure, over or under servicing can be just as damaging. Frequent under servicing can inevitably lead to problems going unnoticed, which can catalyse consequent parts to fail as well. Equally, over servicing can cause just as many problems as with more time spent carrying out unnecessary maintenance, there is a higher chance of unknowingly losing a critical screw, breaking a panel or stripping a bolt.
Evidently, human error can play a crucial part in system or part failure, with production operators critical to the successful operation of machinery. Distraction and tiredness are all common human traits that have a significant impact on performance and avoidable downtime. According to a study by Vanson Bourne, human error caused 23% of all unplanned downtime in the manufacturing industry, while other sectors were as low as 9%.
These human errors, as well as the other common causes of system failure, lead to component issues. Problems such as misalignment (which can trigger component fatigue and failure), corrosion and general surface degradation are all consequent effects of problems that can arise. Therefore, it is the job of the engineer to help prevent component wear and reduce the likelihood of downtime.
How to Choose the Right Material
When picking the right component for the job, there are several factors engineers should take into consideration to help ensure the part is capable of dealing with high-stress.
The first, and probably most important consideration, is the component’s wear resistance – especially within the component’s specific application. Inevitably, all moving components will eventually wear, so by first choosing components that can withstand high loads and frequent usage, engineers will reduce the need for downtime.
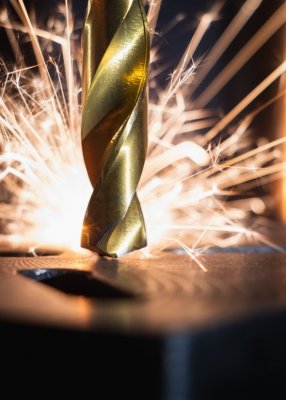
That said, it’s important to take into consideration the application of the component. For example, while copper-based alloys provide superior durability, this material is prohibited from use within parts of food manufacturing. This is predominantly because copper risks corrosion when exposed to any acidic substance, putting processed food at risk of contamination.
Engineers must also consider the use of the component. Machines in need of frequent cleaning with aggressive solutions must be able to cope with the environment it is placed within while also being able to bear high levels of stress. Materials that require low maintenance are also extremely beneficial to companies looking to improve production efficiency, meaning less time is spent reviewing and servicing parts.
Leading the Market
In recent years, we have seen developments in hard-wearing materials capable of bearing high-stress, but none stand out more than the recent adoption of ceramic components.
Ceramic components boast excellent levels of hardness, wear resistance, temperature resistance, impact strength, abrasion resistance and even feature non-stick properties – meaning machinery processes and operations can be made safer and quality-oriented. One industry that has already taken advantage of the material’s robust properties is the tooling industry, where the alternative material offers highly precise application while showing almost no signs of wear, even after heavy use.
The material is also a good choice for applications with demanding mechanical loads due to its high flexural strength and hardness – with norelem’s comprehensive ceramic range specifically designed with service life in mind.
Where hygiene is a top priority, high-grade alloy stainless steel remains set to continue leading the food manufacturing, pharmaceutical and healthcare industries.
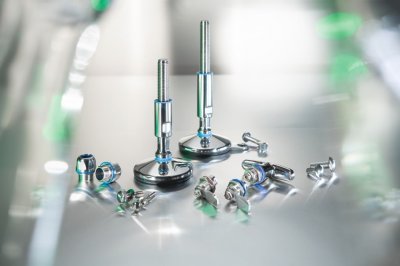
Not only is the material capable of handling high-stress functions due to its inherent durability, but its smooth non-absorbent finish offers a hygienic surface that doesn’t harbour germs or chemicals. With a roughness of Ra 0.8 µm, norelem’s screws and nuts alleviate the issue of peaks and troughs in the metal that could provide a breeding ground for microorganisms. The material is also notably resistant to corrosion and tolerant to extreme changes in temperature, making it one of the most versatile materials on the market.
Where movement is crucial, nothing bears high-stress better than linear actuators. When paired with norelem’s toothed belt drives and profile rail guide, the rail system is capable of absorbing the highest forces from all directions while also featuring good wear resistance. Linear actuators are optimised to move large masses, without the need for continual servicing, providing the perfect solution to transporting heavy loads in an environment where production efficiency is crucial.