To Reduce Waste in Manufacturing, Get Rid of Workarounds
Reducing waste in manufacturing starts by identifying the root cause of quality issues.

Waste reduction is a ubiquitous topic in manufacturing. There are opportunities to reduce waste at every step of production, and so it is everyone’s job.
When InfinityQS quality professionals visit a facility to advise on how to best implement our Quality Intelligence products, data collection is almost always the first place we start. This is a great way to understand how our customers’ processes work. Too often, we find that their processes have many undocumented extra steps added to them.
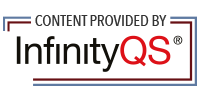
But where do the undocumented, extra steps come from? They’re workarounds—actions developed through experience by the operators that help them get the job done when something’s not quite right. They’re like an open secret; everyone knows about them, but nobody wants to talk about them.
The Hidden Factory
By looking at the nuances of an organization’s processes, our quality professionals are trying to improve their current picture and build a better tomorrow. Creating a process map is the best way to achieve this. But when there are years or decades of one-off workarounds engrained in processes, that becomes a very tough job.
Eventually, so much effort is involved in keeping up the workarounds that it’s as if a second, “hidden factory” is at work on the production floor. No manufacturer is immune to this problem. Even multinational, multibillion-dollar corporations are susceptible to this insidious problem.
An Example of Waste
We once discovered a hidden factory at work on the production floor of a major aircraft manufacturer. The part in question was an interior sidewall panel—the plastic piece that’s part of a commercial airliner’s wall when you sit near a window. Manufacturing these pieces requires molds, materials, layers, resin, and many other parts that all must be added in the right steps.
When they’re near completion, the panels go into an autoclave, sort of a pressurized oven that’s used to cure composite materials. With so much going into them, these panels often experience issues: burn spots, rough areas, delaminating, to name a few. And these issues cause rework, none of which was formally documented.
According to the interior sidewall panel process flow, the pieces are removed from the autoclave, get trimmed, and then they’re pretty much done. No mention of what happens when there’s an issue, or the extra steps that occur when the panel is reworked. That’s waste.
Why Waste Reduction Matters
In most manufacturing operations, management doesn’t make waste reduction a priority. Instead, what they care about is profit. As long as the business is making money, they just don’t have time to devote to worrying about waste. And without top-down pressure to solve problems at the root, hidden factories continue to exist.
But in today’s marketplace—highly competitive, dwindling profit margins, and the high price for failure—every organization needs to take a good, hard look at waste. They need to expose the hidden factory and take care of their processes. It’s the low-hanging fruit of manufacturing quality improvement, and it’s ripe for picking.
When Waste Reduction is Unpopular
Let’s say a company sends its people to a waste reduction training that has the mantra “Zero Defects.” Employees come back fired up to make a difference. They start focusing on reducing waste within their organization.
This initiative seems beneficial, but people higher up the corporate ladder don’t want the waste and inefficiencies exposed. They’re afraid that it will spotlight bad decisions or poor judgment that could make them look bad. So, what’s the end result? The employees who went through the training and want to reduce waste feel like they have no power to make a change. The hidden factory remains hidden.
These folks continue to do their job; they get out the sander and smooth over the rough edges and do what they can to keep the product moving through the line. They’re not scared of calling out waste; instead, they think, “Well, that’s what I’m paid to do. I’m paid by the hour.” Or, “It doesn’t happen in my area. I don’t want to get someone upstream or downstream in trouble.”
This tacit motivation to remain quiet will continue until the mindset of management changes to something more encouraging. Unless management is on board with waste reduction initiatives and empowers people to expose the hidden factory, it will remain unseen.
Reducing Waste Improves Your Bottom Line
Waste reduction efforts can directly affect your bottom line. Take, for example, an airplane manufacturer supplier that builds a small flap for horizontal stabilizers. Horizontal stabilizers are the flat pieces across the back of an airplane that, unsurprisingly, help stabilize it.
The airplane manufacturer began an initiative to reduce variation in the stabilizers. This came about because when the flaps were received from the supplier, they encountered issues when attaching them. The flaps had so much variation in their attachment points that the attachment pins weren’t fitting properly.
The Problem with Workarounds
A workaround was developed. The stabilizers were placed in an assembly fixture so that “shims” could be put in certain places to get all the pins to align properly.
Then, as part of a cost-reduction effort, an automated shim-making machine was implemented. This allowed for some direct feedback for what shim size to make, which sped up production. Cycle times were improved, but this was just another workaround, and another type of waste.
Because of variation, the flaps didn't fit when they arrived. This led to adding the shim-making step, which led to the automated shim-making machine. However, orders were coming in so fast that even with these “improvements” the manufacturer was only just keeping up with orders.
By the time our team was called, the manufacturer had made a decision on how they would meet demand. Instead of fixing the cause of the problem, their “solution” was to build another assembly fixture in order to shim more stabilizers. You can see how these workarounds add up.
The Solution
As quality professionals and consultants, our team was able to make further-reaching recommendations than the manufacturer’s frontline employees. We immediately set out to identify the source of variation at the supplier—that was obviously the root cause. In this case, the root cause was the variation in the flaps that attached to the larger stabilizer.
We were able to reduce and eliminate a lot of variation being introduced at the source. The result was that, going forward, only one shim machine was needed to increase the production rate and keep up with demand. That’s 1) a big money-saver for the company, and 2) a time-saver for the production people. A win-win.
If we can focus on discovering root causes and eliminate variations at the source, we can eliminate many of the added costs that creep into our production processes. These variations are usually the result of people trying to fix something quickly or make the best of a deteriorating situation.
The airplane manufacturer was finally able to fix their problem because they were open to waste reduction initiatives. They recognized the issues and put a quality team on the case. There’s no reason to leave money on the table by ignoring waste. Companies need to recognize what’s there, pursue intelligent fixes, and the bottom line will reflect their efforts.
If you’re ready to start a waste-reduction initiative, see how state-of-the-art SPC from InfinityQS reduces waste in manufacturing.